
Process Improvement Limitations: Scale, Structure, Sustainability

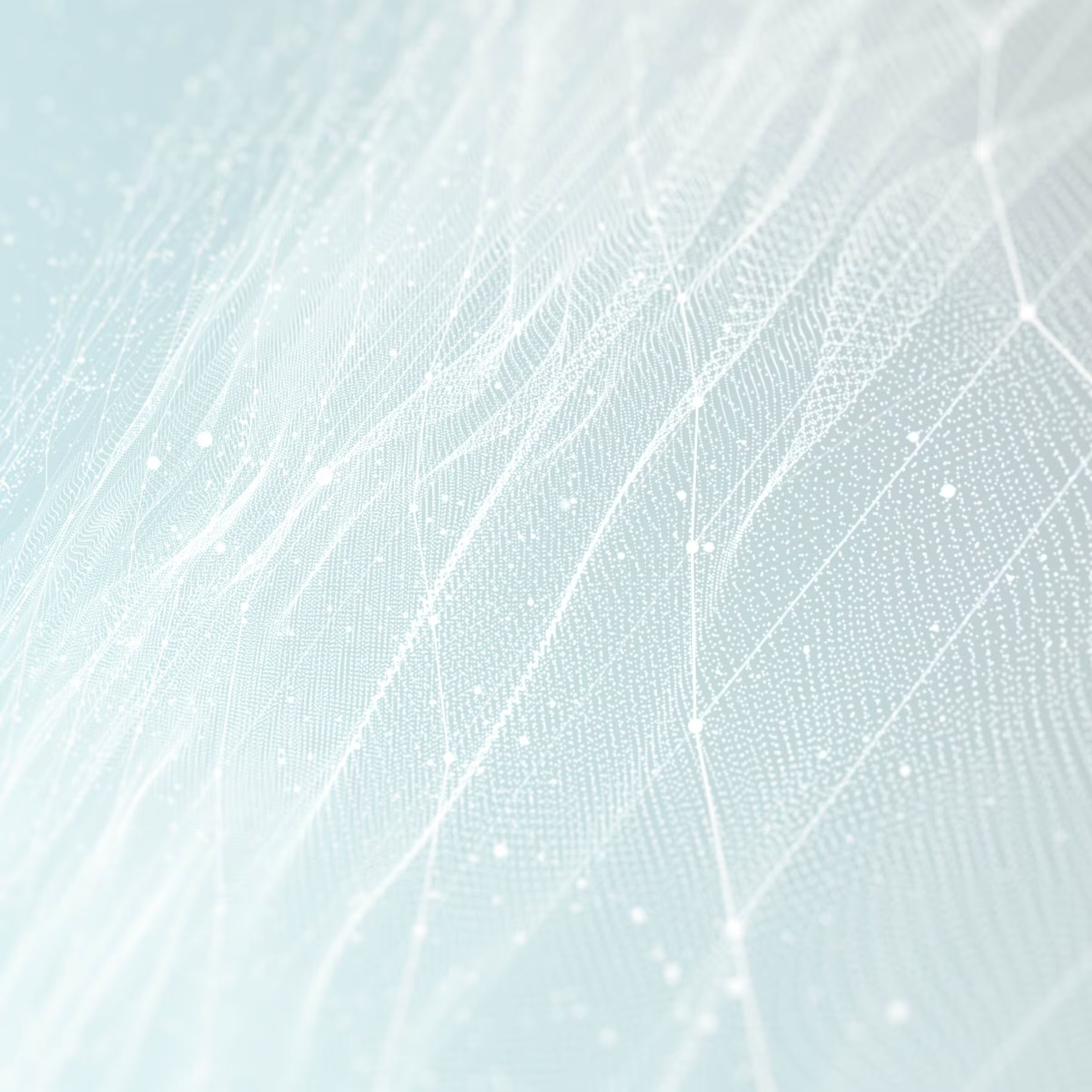
Recently, Craig Seebach, VP, Enterprise WFO at Verint, moderated a webinar, “Creating Tremendous Results at Speed,” with Caroline Basyn, SVP, Global Business Services at Mondelez, the global snack manufacturer (Oreo and Cadbury brands to name a couple).While many topics were covered, improving processes came up a number of times with three key observations:
- Improving processes on a global scale is difficult due to limited Lean/Six Sigma teams and a lack of end-to-end process visibility
- Structure needs to be in place to assess the processes, determine the value and expected results of improving or automating them, and prioritize according to the potential impact of the changes on the organization
- Once the changes are made, measures need to be in place to monitor adoption and help ensure the sustainability of the changes and achievement of desired business outcomes.
Following is the first of three blogs in this series, each addressing one of the three key observations.
Hundreds of Processes: How Do Global Organizations Scale Improvements?
Many large companies have a core team of Lean and/or Six Sigma black belts charged with improving processes across their organization. They move from function to function typically addressing processes that are considered broken—they fix a process and move on to the next.
This approach presents a number of challenges.
First, processes in one function often impact another function. Similar to popular stress balls, contracting one area pushes out/creates force in another area. Without end-to-end visibility into processes across the organization, a fix in one area can create stress in another.
Second, not all “broken” processes are readily evident. Oftentimes work has been processed the same way for a number of years. Goals are being met, but is the process as efficient as it could be?
We often find “hidden capacity” when we analyze process flows with data captured directly from the employee desktop. The opportunities for improvement are abundant but dormant, because the process itself is not causing organizational pain.
Third, just because the Six Sigma team comes in and redesigns a process doesn’t mean the process will be followed. Old habits die hard. Companies could benefit significantly from a means of measuring process adoption and motivating employees to change their behaviors to process the work as prescribed.
See how the largest U.S. non-profit health insurer improved operational performance.
One way to optimize and scale your Lean and Six Sigma resources is with Desktop and Process Analytics solutions that can capture activity directly from the employee desktop (no integration with core systems required), map these activities to processes, and create a visual map of the processes that highlights both bottlenecks and best practices. The process maps can span users and functions from the beginning to end of a process.
The team not only has a visual representation of as-is processes to help identify where improvements are needed, but the same maps can be used after process changes have been implemented to monitor whether or not employees are following the new process steps. By seeing the near real-time process maps, Lean and Six Sigma resources have a means of quickly analyzing cross-functional and enterprise-wide opportunities for improvement.
Look for the next blog in this series, “Hundreds of Processes: How Do You Prioritize for Streamlining and Automation?”